Background
The exciting field of smart materials is expanding rapidly, with one of the most interesting areas being that of shape memory alloys. A shape memory alloy (SMA) can undergo substantial plastic deformation, and then be triggered into returning to its original shape by the application of heat. These properties have led to a proliferation of diverse applications in a variety of industries, see table 2.
From early applications such as greenhouse window openers in which an SMA actuator provided temperature-dependent ventilation, through to plastic-coated mobile phone antennas made from a super-elastic SMA capable of recovering its shape even after an extreme deformation such as dropping the phone, the list of applications has increased enormously throughout the 1990s. Medical applications of SMAs, using their superelastic and shape recovery properties, are particularly interesting and beneficial, and are growing rapidly.
History
Surprisingly for materials with so many applications, shape memory alloys have not been around a long time. A key discovery occurred in 1962, when a binary alloy composed of equi-atomic nickel and titanium was found to exhibit a shape recovery effect when heated after being mechanically deformed. Although other reversible phase change materials were known at the time, the Ni-Ti alloys showed a large recoverable strain value when compared to other binary, ternary or quaternary shape memory alloy systems.
The physical performance of the Ni-Ti alloy made it a landmark discovery, and the range of commercially viable applications that have been found for the materials is proof of the importance of the nickel-titanium shape memory alloys. But the discovery may have been a happy accident. Rumour has it that William Buehler, who was working with high nickel-bearing alloys for gas turbine components, left a small ingot of Ni-Ti alloy made in a vacuum melt furnace on a desk in direct sunlight. When Buehler and his colleagues came back from lunch, they noticed the ingot’s shape had changed. Now known as Nitinol (derived from Ni-Ti Naval Ordinance Laboratories, part of the US Department of Defence), the name has become one of the commonly used titles for the SMAs emanating from Buehler's laboratory.
Alloy Types
Since the discovery of Ni-Ti, at least fifteen different binary, ternary and quaternary alloy types have been discovered that exhibit shape changes and unusual elastic properties consequent to deformation. Some of these alloy types and variants are shown in table 1.
Table 1. Shape memory alloy types.
· Titanium-palladium-nickel · Nickel-titanium-copper · Gold-cadmium · Iron-zinc-copper-aluminium · Titanium-niobium-aluminium · Uranium-niobium · Hafnium-titanium-nickel | · Iron-manganese-silicon · Nickel-titanium · Nickel-iron-zinc-aluminium · Copper-aluminium-iron · Titanium-niobium · Zirconium-copper-zinc · Nickel-zirconium-titanium |
The original nickel-titanium alloy has some of the most useful characteristics in terms of its active temperature range, cyclic performance, recoverable strain energy and relatively simple thermal processing. Ni-Ti and other alloys have two generic properties thermally induced shape recovery and super- or pseudo-elasticity. The latter means that an SMA in its elastic form can undergo a deformation approximately ten times greater than that of a spring-steel equivalent, and full elastic recovery to the original geometry may be expected. This may be possible through several million cycles. The energy density of the alloy can be used to good effect to make high-force actuators - a modern DC brushless electric motor has a mass of 5-10 times that of a thermally activated Ni-Ti alloy, to do the same work.
The superelastic Ni-Ti alloys are “stressed” by simply working the alloy. These stresses can be removed, just as with many other alloys, by an annealing process. The stressed condition is termed stress-induced martensite, which is the equivalent of being cold/hot worked.
SMAs, particularly nickel-titanium, are commercially available from several sources. However, world production is small compared to other metal commodities (about 200 tonnes were produced 1998) owing to difficulties in the melt/forging production process, and so the cost of the material high US$0.30-US$1.50 (UK£0.20-£1.00) per gram for wire forms 1999 prices). Fortunately, most current applications require only small amount of the material. As world production increases (as it has done quite dramatically in the 1990s) so prices should decrease. Wires, strip, rod, bar and sheet are all readily available and alloy foams, sintering powders and sputtering targets of high purity are also produced.
Medical Applications
The variety of forms and the properties of SMAs make them extremely useful for a range of medical applications. For example, a wire that in its “deformed” shape has a small cross-section can be introduced into a body cavity or an artery with reduced chance of causing trauma. Once in place and after it is released from a constraining catheter the device is triggered by heat from the body and will return to its original “memorised” shape.
Increasing a device’s volume by direct contact or remote heat input has allowed the development of new techniques for keyhole or minimally invasive surgery. This includes instruments that have dynamic properties, such as miniature forceps, clamps and manipulators. SMA-based devices that can dilate, constrict, pull together, push apart and so on have enabled difficult or problematic tasks in surgery to become quite feasible (See Table 2. for medical and other applications).
Table 2. Current examples of applications of shape memory alloys.
· Aids for disabled · Aircraft flap/slat adjusters · Anti-scald devices · Arterial clips · Automotive thermostats · Braille print punch · Catheter guide wires · Cold start vehicle actuators · Contraceptive devices · Electrical circuit breakers · Fibre-optic coupling · Filter struts · Fire dampers · Fire sprinklers · Gas discharge · Graft stents · Intraocular lens mount · Kettle switches · Keyhole instruments · Key-hole surgery instruments | · Micro-actuators · Mobile phone antennas · Orthodontic archwires · Penile implant · Pipe couplings · Robot actuators · Rock splitting · Root canal drills · Satellite antenna deployment · Scoliosis correction · Solar actuators · Spectacle frames · Steam valves · Stents · Switch vibration damper · Thermostats · Underwired bras · Vibration dampers · ZIF connectors |
Stents
The property of thermally induced elastic recovery can be used to change a small volume to a larger one. An example of a device using this is a stent. A stent, either in conjunction with a dilation balloon or simply by self-expansion, can dilate or support a blocked conduit in the human body. Coronary artery disease, which is a major cause of death around the world, is caused by a plaque in-growth developing on and within an artery’s inner wall. This reduces the cross-section of the artery and consequently reduces blood flow to the heart muscle. A stent can be introduced in a “deformed” shape, in other words with a smaller diameter. This is achieved by travelling through the arteries with the stent contained in a catheter. When deployed, the stent expands to the appropriate diameter with sufficient force to open the vessel lumen and reinstate blood flow.
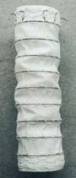 |
Figure 1. A reinforced graft for vascular application to replace or repair damaged arteries (25mm diameter). |
The same technique can be employed in many of the body's conduits, including the oesophageus, trachea, biliary system and urinary system. The technology of self-expansion or balloon-assisted expansion is used for many millions of these stents each year and the numbers are steadily increasing.
Introducing a catheter directly through the complex arterial channels via a small external incision is generally not possible, owing to the relative rigidity and lack of steerability of the catheter alone. To ensure that the catheter gets to the correct site, a guide-wire must first be introduced. Superelastic Ni-Ti alloys are used very successfully for this application. Their torquability, deformability, recovery and low whipping effect allow the surgeon to get the highly flexible guide wire in place. The end of the guide wire is fed through a central or side hole in the catheter. The catheter can only go where the guide wire is positioned - it acts like a railway line. Often, the guide wire may be kept in place while other catheters for different tasks use the same guide wire.
Vena-cava Filters
Vena-cava filters have a relatively long record of successful in-vivo application. The filters are constructed from Ni-Ti wires and are used in one of the outer heart chambers to trap blood clots, which might be the cause of a fatality if allowed to travel freely around the blood circulation system. The specially designed filters trap these small clots, preventing them from entering the pulmonary system and causing a pulmonary embolism. The vena-cava filter is introduced in a compact cylindrical form about 2.0-2.5mm in diameter. When released it forms an umbrella shape. The construction is designed with a wire mesh spacing sufficiently small to trap clots. This is an example of the use of superelastic properties, although there are also some thermally actuated vena cava filters on the market.
Dental and Orthodontic Applications
Another commercially important application is the use of superelastic and thermal shape recovery alloys for orthodontic applications. Archwires made of stainless steel have been employed as a corrective measure for misaligned teeth for many years. Owing to the limited “stretch” and tensile properties of these wires, considerable forces are applied to teeth, which can cause a great deal of discomfort. When the teeth succumb to the corrective forces applied, the stainless steel wire has to be re-tensioned. Visits may be needed to the orthodontist for re-tensioning every three to four weeks in the initial stages of treatment.
Superelastic wires are now used for these corrective measures. Owing to their elastic properties and extendibility, the level of discomfort can be reduced significantly as the SMA applies a continuous, gentle pressure over a longer period. Visits to the orthodontist are reduced to perhaps three or four per year.
This continuous, gentle, corrective force illustrates the rather odd elastic properties of superelastic SMAs. A graph showing extension plotted against load produces a straight, horizontal line after initial loading. This shows the alloy to be non-Hookean, unlike carbon steel and other springs and constant forces can be derived from springs made of Ni-Ti alloy.
Apart from the tensioned archwires, other superelastic orthodontic devices exist which can move teeth linearly where there is uneven tooth spacing. Movements of 6mm in 6 months are possible with minimum discomfort. Devices also exist that can apply torsional forces in the case of a “twisted” tooth. Orthodontists have modular kits, in which adhesively bonded brackets are attached to the teeth and the arch wire is then attached to and guided by the bracket. Other wire-forms can then be fitted to the brackets to push, pull, twist or force other movements that facilitate corrective measures for cosmetic or clinical reasons.
Such dental SMA devices have proved very successful in trials and are being made commercially available in Europe. Other similar SMA devices are also being used for healing broken bones - staples of the shape memory materials are attached to each part of the bone, and these staples then apply a constant, well-defined force to pull the two pieces together as the SMA is warmed by the body and tries to return to its original configuration. This force helps knit the two pieces of bone back together. Such smart ‘healing’ powers are the reason why SMAs are being borne in mind for many applications in the medical, dentistry and other fields in the future.