Background
It might not be what you would normally call a ‘smart’ material, but copper is certainly helping to pack more intelligence on to the average microchip. The material is now being used by IBM, soon to be followed by the other big chip manufacturers, to produce the delicate circuitry on its silicon wafers. The outstanding improvements that will become the future norms speak for themselves. Chips that run four times faster, chips with connections less than half the size of those available now and, unbelievably, chips that are even smaller will become common. Moore’s Law, which states that the density of transistors packed on a single computer chip will double every 18 months, is being upheld by one of the oldest metals known.
Copper vs. Aluminium
All of which begs the question - if copper is such a good material for making circuitry on chips, why wasn’t it used in the first place? Until now, aluminium has held sway despite being a poorer electrical conductor and thermal conductor. Yet aluminium had one property which copper did not - it did not diffuse into the silicon semiconductor material used to make the chips.
Copper and Silicon Chips
Diffusion of stray metal ions into silicon chips spells disaster for the semiconductor material, which is poisoned by the foreign ions. When chips were first being produced, chip manufacturers discovered that copper ions diffused from the metal circuitry into the silicon, and so couldn’t be used. Silicon scientists have been working on a way to prevent this diffusion for many years.
August 1997, saw Sematech, a research and development group of the leading chip manufacturers, announced that it had succeeded in isolating copper from silicon. A month later, IBM announced its own manufacturing process based on the technology, replacing traditional aluminium with copper. IBM thinks that CMOS 7S, as the technology is known, will allow it to build higher performing, higher functioning microprocessors for computer systems, figure 1, and also allow other manufacturers to create smaller, lighter electronics devices that need less power to run.
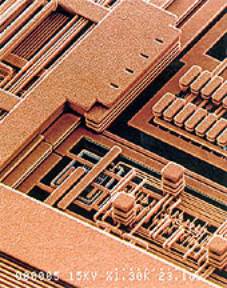 |
Figure 1. Scanning electron microscope image of IBM’s six-level copper interconnect technology (copyright IBM Corporation) |
Advantages of Copper
Copper enables this by virtue of its superior electrical and thermal properties. As it is a better conductor of electricity than aluminium, copper interconnections can be made narrower - 0.1 microns instead of 0.25 microns. IBM says that the circuitry on the new chips will be built to dimensions of 0.2 microns, allowing for up to 12 million gates on a single chip. Altogether, CMOS 7S can pack 150-200 million transistors on a single chip, which translates as a big increase in computing power.
Implications of Smaller Chips
Such close packing is only possible because copper conducts heat very well, preventing damage to the circuits from overheating. Not that there is as much danger of that anyway - transistors based on the CMOS 7S technology operate at only 1.8 volts, allowing very low power operation. Devices based on the technology should be less of a drain on their batteries, or require less weighty power packs. Portable computers, mobile phones and personal digital assistants could all lose weight thanks to the copper-based chips.
Structure of the CMOS 7S Chips
As figure 2 shows, CMOS 7S is an intricate technology. Six layers of metal are laid down on each chip, allowing complex circuit design. But just how Sematech and IBM in particular managed to do this without poisoning the semiconductor remains a secret - understandably, given the massive potential market for devices based on copper technology.
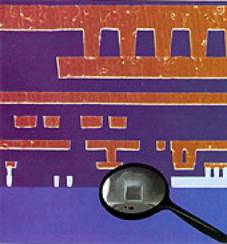 |
Figure 2. SEM cross-section of CMOS 7S copper process, showing the six copper levels used for chip wiring and one tungsten level for local interconnect. Inset shos 0.16 micron effective channel length, an impressive size reduction over current technology (copyright IBM Corporation) |
Applications for the CMOS 7S Chips
IBM Microelectronics has already introduced its next generation of application-specific integrated circuits (ASICs) based on CMOS 7S. The company is also producing design tools and services to assist other electronics manufacturers in building their own products. Such design kits are aimed at helping developers of computers, communications equipment and consumer electronics improve the function of their products through the use of copper. The kits will enable the manufacture of ASICs designed to perform functions such as manipulating 3D graphics or controlling digital cameras. ASICs are already widely used to give computer intelligence to everything from electronic games to telephone switching systems.
Implications for the Copper Industry
So what will all this mean for the world consumption of copper? Unfortunately for the industry, not a lot. Despite the fact that millions of chips are sold each year and that this figure is expected to increase rapidly, the amount of copper material needed in each chip can be measured in the order of micrograms. But the prestige is important, according to Robert Payne, president of the Copper Development Association. ‘It’s the advanced technology provided by copper that is important,’ he said, ‘not the weight consumed.’